The Essential Duty of Container Welding Assessment in Ensuring Structural Stability and Security Conformity in Industrial Applications
In the realm of commercial applications, tank welding assessment emerges as an essential element in protecting architectural integrity and making sure compliance with security regulations. Using a mix of techniques such as visual assessments and advanced testing approaches, these assessments offer to identify and alleviate possible flaws before they intensify right into significant risks.
Relevance of Tank Welding Assessment
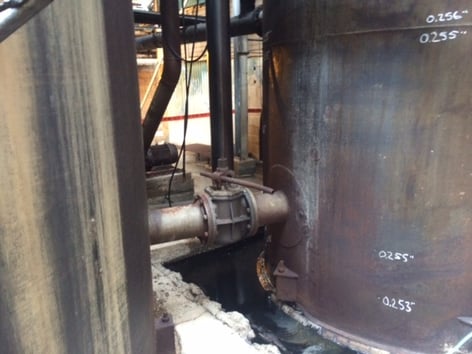
Making sure compliance with market requirements and guidelines is an additional substantial facet of container welding evaluation. Regulative bodies mandate stringent guidelines for the building and maintenance of tank, and complete examinations aid companies abide by these needs. Non-compliance can cause extreme fines, consisting of penalties and shutdowns, even more emphasizing the need for rigorous evaluation procedures.
In addition, container welding examination plays a critical role in keeping operational effectiveness. In recap, the significance of tank welding examination lies in its capacity to protect public health, secure the environment, and make sure conformity with regulative frameworks.
Secret Inspection Strategies
Reliable tank welding examination relies upon a selection of key techniques that make sure comprehensive examination of weld top quality and structural stability. Among the most common methods are aesthetic examination, ultrasonic testing, radiographic testing, and magnetic bit screening - Tank Welding Inspection. Each approach offers distinct benefits in analyzing various aspects of the weld
Visual assessment acts as the initial line of defense, permitting assessors to determine surface area issues, irregularities, or disparities in the weld bead. Ultrasonic testing utilizes high-frequency acoustic waves to detect interior problems, such as splits or gaps, giving a comprehensive assessment of weld integrity. This method is particularly effective in identifying issues that may not show up on the surface.
Radiographic screening makes use of X-rays or gamma rays to generate photos of the welds, disclosing internal stoppages and providing a long-term document for future referral. This strategy is very efficient for important applications where the danger of failure should be minimized.
Lastly, magnetic particle screening is used to determine surface and near-surface problems in ferromagnetic materials. By using electromagnetic fields and fine iron bits, examiners can pinpoint suspensions that might endanger the architectural stability of the tank. With each other, these strategies develop a durable framework for guaranteeing top quality welds in commercial applications.
Conformity With Security Standards

Regular inspections play a critical function in guaranteeing conformity by identifying potential failures or deviations from suggested requirements. Inspectors are trained to review weld high quality, validate material requirements, and evaluate the total architectural integrity of containers. Their know-how is important in making certain that welding processes satisfy the called for security requirements.
Moreover, compliance with safety requirements not just protects workers yet also safeguards the atmosphere from possible hazards such as leaks or disastrous failings. Organizations that prioritize security conformity are better positioned to alleviate threats, enhance operational effectiveness, and promote a culture of security within their labor force. In recap, preserving rigorous compliance with safety and security standards is important for the effective procedure of storage tank welding tasks in commercial setups.
Benefits of Regular Evaluations
Routine assessments are indispensable to maintaining the structural integrity and security of bonded containers. These inspections provide a systematic method to determining prospective flaws or weak points in the welds, making sure that any kind of issues are dealt with before they escalate into significant failures. By performing regular analyses, organizations can detect corrosion, tiredness, and other forms of wear and tear that may compromise tank efficiency.
In addition, regular examinations add to compliance with sector guidelines and requirements. Abiding by these guidelines not only minimizes lawful dangers however also enhances the company's reputation for safety and integrity. Routine evaluations foster a proactive safety and security society, encouraging employees to identify and prioritize the value of devices integrity.

Study and Real-World Applications
Situation researches and real-world applications illustrate the concrete influence of effective tank welding assessment practices. Following the application of strenuous welding inspection methods, including visual and ultrasonic screening, the center identified vital problems in weld joints that could have led to devastating failings.
In a similar way, a water therapy plant executed a comprehensive evaluation program for its storage tank welding procedures - Tank Welding Inspection. By including look these up non-destructive testing approaches, the plant had the ability to identify very early signs of corrosion and tiredness in weld joints. This prompt treatment expanded the life-span of the tanks and ensured compliance with safety policies, therefore securing public health and wellness
These situation studies underscore the importance of regular and systematic tank welding evaluations. By prioritizing these practices, industries can mitigate risks, enhance structural honesty, and ensure conformity with safety and security criteria, eventually causing improved functional performance and lowered responsibilities.

Final Thought
In verdict, tank welding examination is an important part of preserving architectural integrity and safety and security in industrial applications. Utilizing various assessment strategies ensures very early discovery of potential problems, consequently preventing tragic failings.